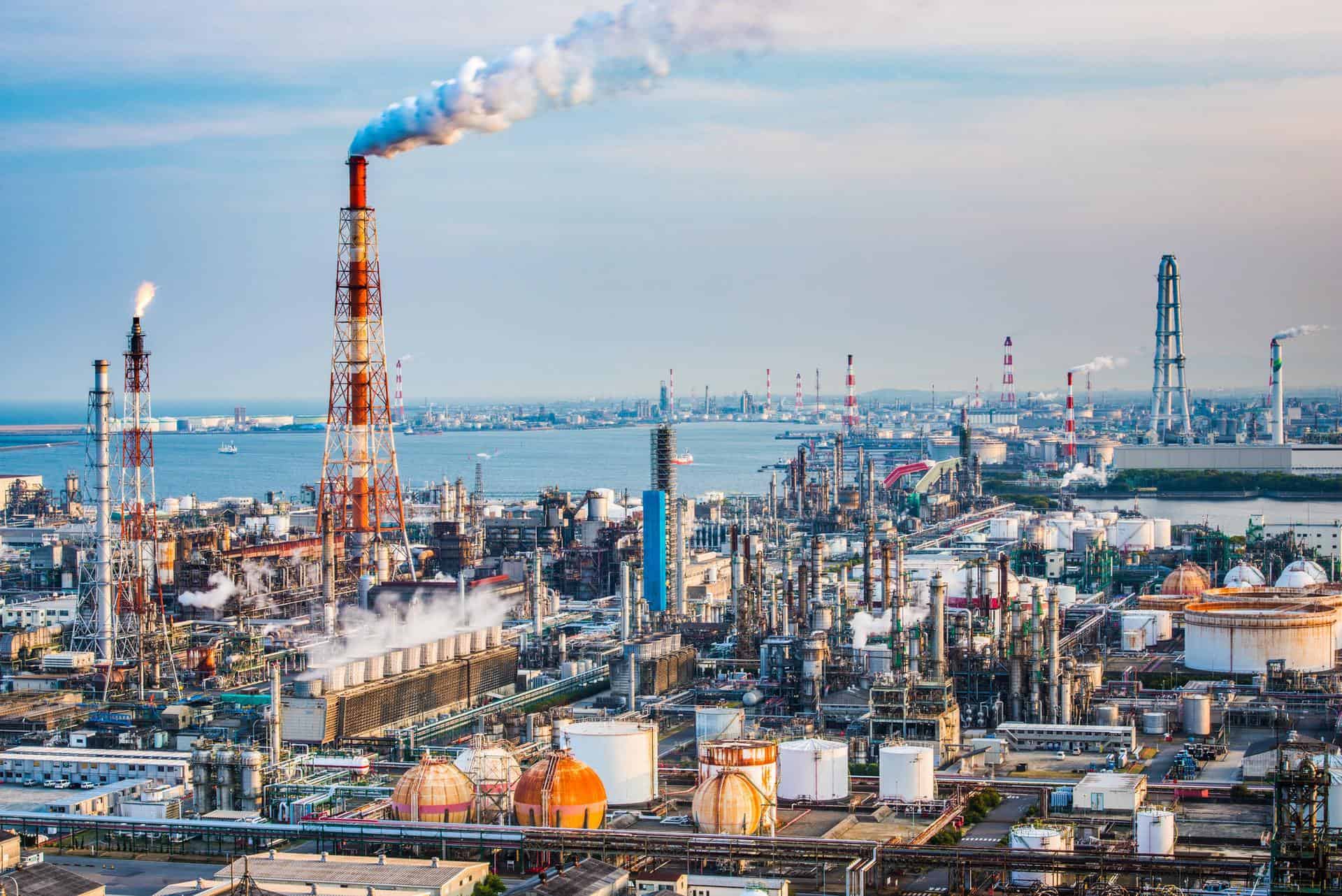
Industry Achievements: Petrochemical Industry
Increase of production capacities and realization of predictive maintenance through a decision-making information management system & manufacturing and operation management system.
Customer Bottlenecks
Difficulties in the integration of production histories:
Since most production data is recorded by hand, tracing of production histories in case of quality abnormalities is difficult due to the lack of integration of process and quality data.
Impact of quality abnormalities on delivery schedules:
In view of the fact that production is a time-consuming process, rework of a whole batch due to quality abnormalities not only leads to raw material waste but also affects all involved delivery schedules.
Inability to enhance utilization rates and output volumes:
Lack of an accurate understanding of effective equipment usage conditions and control of the whole process from order acceptance to shipping and delivery hinders improvement of utilization rates and output volumes.
High energy costs:
Rising costs of energy resources including water, electricity, and gas result in rising operating costs.
Impact of sudden equipment malfunctions on production capacities:
Sudden malfunctions of key production equipment result in production line shutdowns and serious impacts on output volumes.
Adoption of IIoTFab’s PIMS and MOM.
Plant Information Management System, PIMS:
Real-time production line data are collected at a frequency of ten seconds per instance and process & production information is integrated with ERP and work orders. Hand-written records have been replaced with production histories in electronic format to enable relevant personnel to carry out abnormality root cause analysis and quality controls in a highly efficient manner.
Process quality forecasts and instructions for optimized operations:
Experiences of senior craftsmen are converted into digital format through data analysis and instructions for optimized operations are provided based on the results of model forecasts for compliance by employees to realize the dual goal of stable product quality and output.
Manufacturing and operation management system:
Relevant information on OEE (Overall Equipment Effectiveness), utilization rates, capacity efficiency, yield rates, overall production capacities, and downtime is provided via the production capacity dashboard to give managers a firm grasp of effective equipment usage conditions and production completion rates.
Energy management platform:
This platform integrates decentralized shared systems and “three waste” (water, gas, and solids) treatment systems in a structured manner. Actual operation parameters are controlled through an increase of monitoring points with the goal of reducing energy consumption.
Predictive equipment maintenance:
Predictive models have been established through in-depth analysis. The system is capable of autonomous predictions of equipment reliability as well as the likelihood and occurrence time of future equipment damage, which enables relevant personnel to perform part replacement or maintenance in a predictive manner and thereby extend equipment service life and reduce the costs of excessive maintenance.
Benefits of system adoption
- The platform ensures an effective grasp of production conditions and key factors affecting quality/output. This has resulted in a significant reduction of hand-written records and shortening of data tracing times coupled with an increase of the data tracing efficiency to 95%.
- Data analysis methods are utilized to assist relevant personnel in the systematic management of product specifications and product parameter settings. By observing the instructions issued by the expert system, relevant personnel are able to create conforming products in an effortless manner. This has generated annual manpower and production savings of 50% in addition to capacity enhancements of 8% and an output value increase of around NT$100 million.
- The production capacity dashboard gives managers a full grasp of scheduling and equipment utilization conditions in plants. Decisions and arrangements can be made immediately for equipment with relatively low OEE to achieve OEE improvements (average monthly OEE can be increased by 5%).
- Data collection and real-time monitoring has been implemented for important shared equipment in plants. For instance, annual energy cost savings of around NT$7 million can be achieved though the increase of temperature monitoring points and control of actual operating temperatures and heavy oil consumption for the waste gas boilers of a certain customer.
- Rigorous monitoring of important equipment operation data (e.g., electric currents, rotations, vibrations) has been implemented. Forecasts of equipment deterioration through data analysis modules enable the company to realize the benefits of predictive maintenance and thereby significantly reduce the incidence of sudden malfunctions by 70%.
.