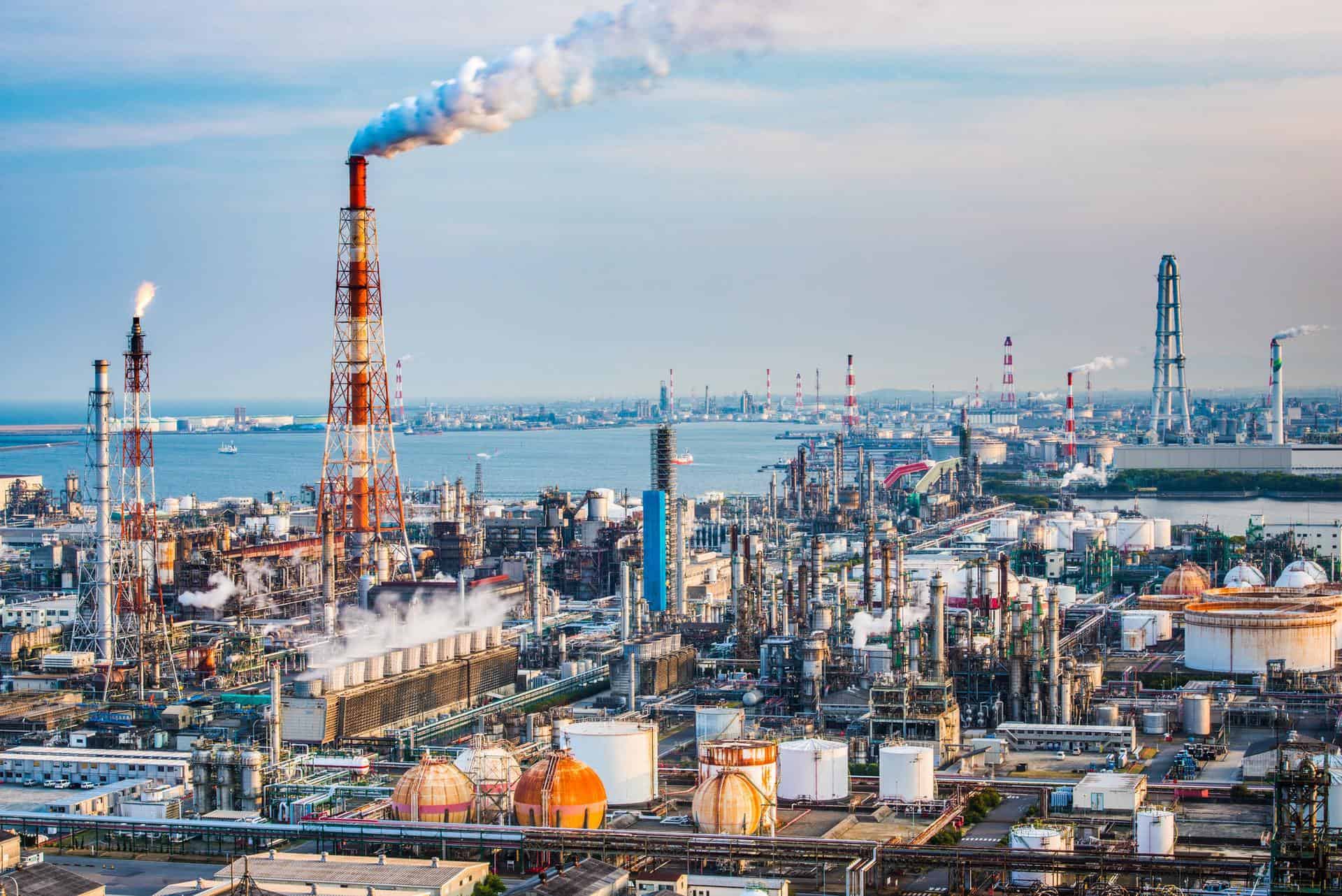
實現AIoT數據分析,提高良率並降低相關營運成本!
生產數據仰賴人工抄寫,品質發生異常時,因製程資料與品質資訊未整合,致生產履歷追溯困難。
每批產品所需生產時間長,當品質發生異常導致需整批重做,不只原料浪費,更是影響到整個所有交貨排程。
無法準確得知設備有效利用的情況與控管接單到出貨的時間,使稼動率及產量難以提升。
現今不管是水、電、氣…等,各種能源成本越來越高,造成營運成本越來越高。
關鍵生產設備臨時故障,造成產線停擺,對產量造成重大損失。
以10秒/次頻率收集產線的實時數據,將製程生產資訊與ERP、工單相整合,以電子生產履歷取代人工抄表,讓人員能以高效率的方式完成異常根因分析與品質管控。
藉由數據分析將老師傅的經驗數位化,由模型預測之結果提供最佳化作業指示讓人員遵循,達到穩定產品品質與產出之效益。
提供設備綜合效率OEE、稼動率、產能效率、良率、完整產能資訊與停機資訊於產能儀表板中,協助管理者確實掌握設備有效利用情形與生產完成率。
將各自分散的公用系統、三廢處理系統以結構化方式整合,藉由增加監控點管制實際運轉參數以減少能耗之用量。
藉由深度分析建置預測模型,系統自主預測設備可靠度、未來設備損壞的可能性與時間點,讓人員可以預期性的進行零件更換或維修,以延長設備壽命與減少過度保養成本。
透過平台即有效掌握生產狀況與影響品質/產出的關鍵因子,大幅減少人工抄寫與縮短資料追溯時間,人員資料追溯效率提升95%。
透過產能儀表板,管理者可完整掌握廠內排程與設備稼動情形,對於OEE較低之設備可馬上進行決策安排以達OEE提升,平均月OEE可提升5%。
針對工廠內重要的公用設備,進行資料收集與即時監控。以某客戶的廢氣爐為例,藉由增加溫度監控點,管制實際操作溫度及重油使用量,有效節省能耗成本約700萬元/年。